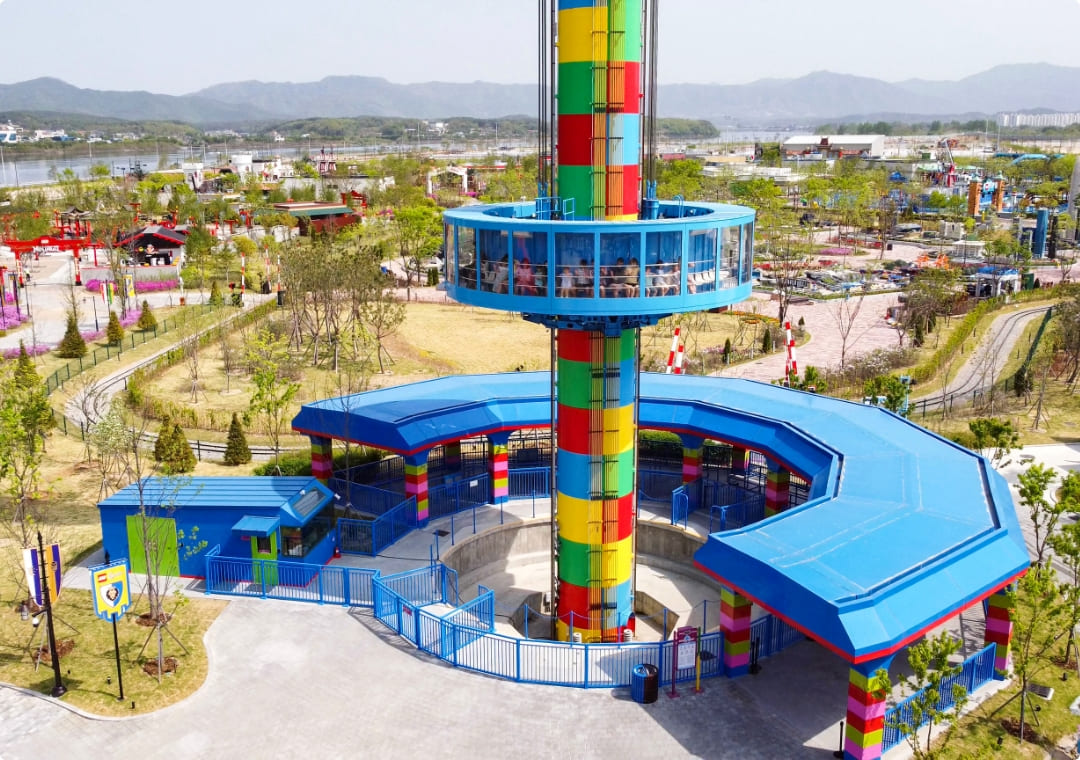
Reach the Height of 59m & Enjoy
Spectacular View of the Dream-filled Land!
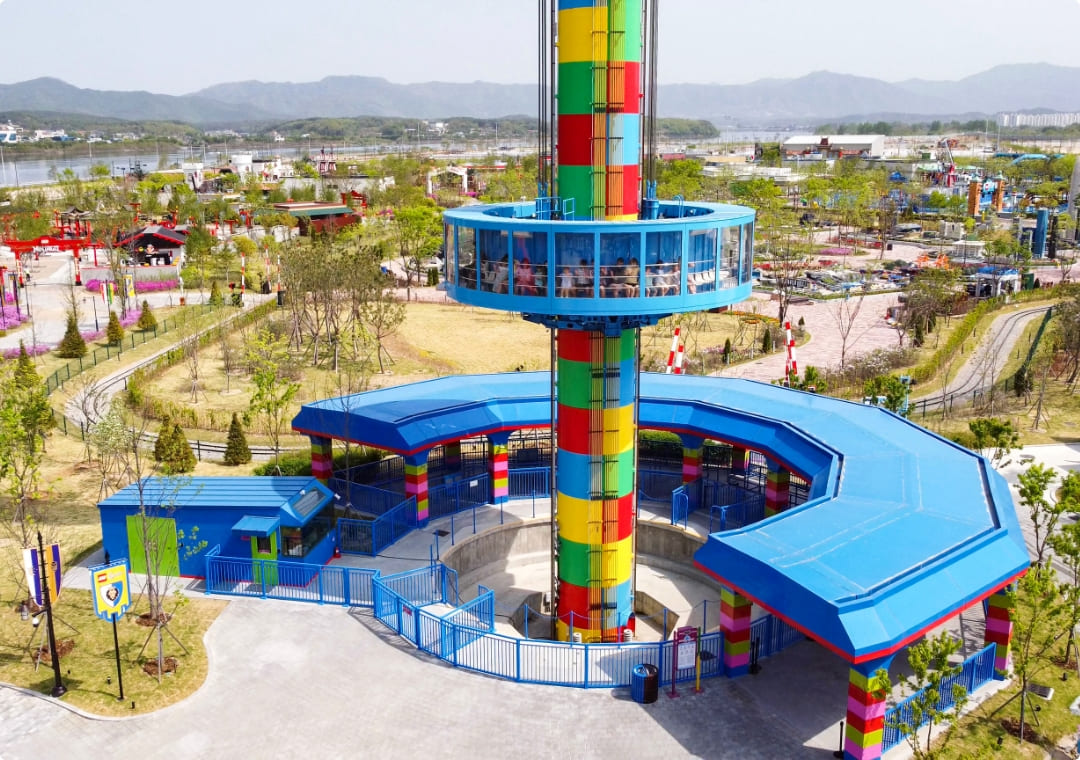
LEGOLAND® KOREA RESORT (Chuncheon, South Korea) is a dream-filled theme park where “play,” “learning,” “creativity,” and “experience” come together. Among its attractions, the Observation Tower, delivered by Sansei Technologies, offers a 360-degree view of the park and its beautiful surroundings from a height of approximately 59 meters, allowing visitors to fully immerse themselves in the LEGOLAND® world.
The tower ride, themed with LEGO bricks offers a special experience for all visitors as a landmark of the park. Just seeing it heightens the excitement, and the adventure begins the moment you head toward the tower.
This is a behind the scenes story of Sansei members who helped the project all the way through from designing to installation.
Project Members
M.T
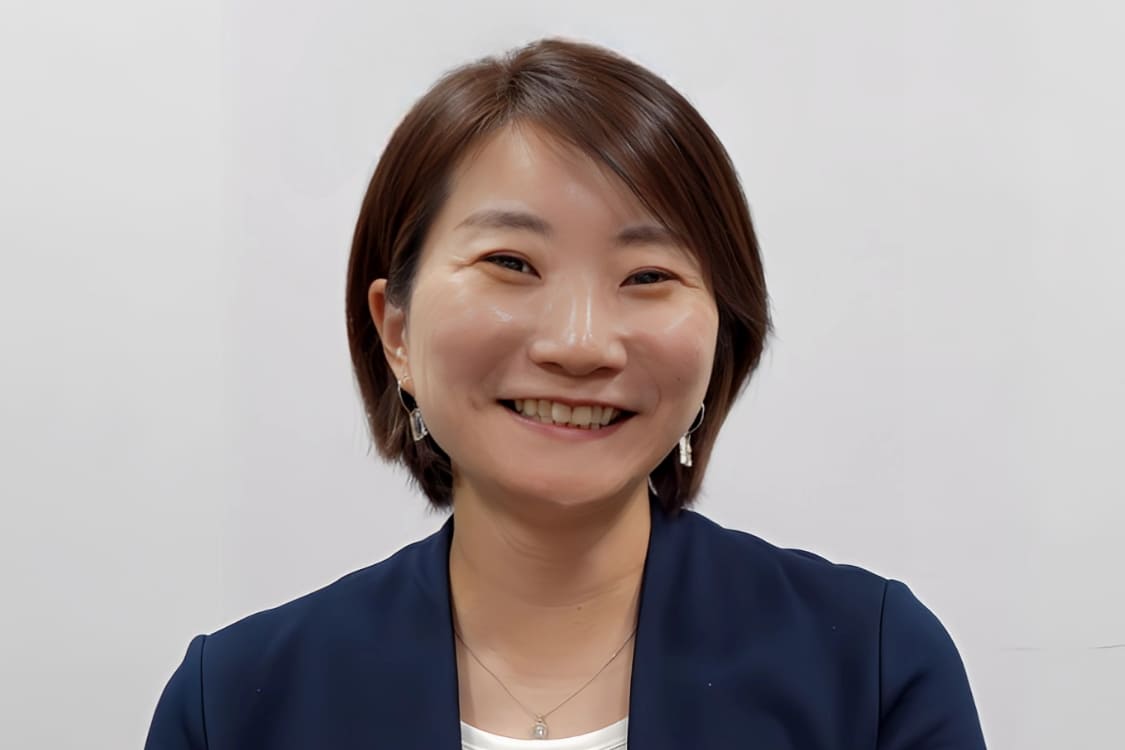
Project Manager
Controlled project work schedule and budget, negotiated with client as Sansei representative, and coordinated internal team and departments.
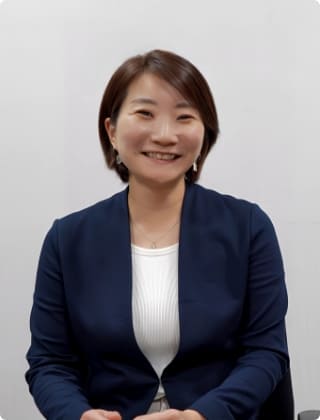
Y.T
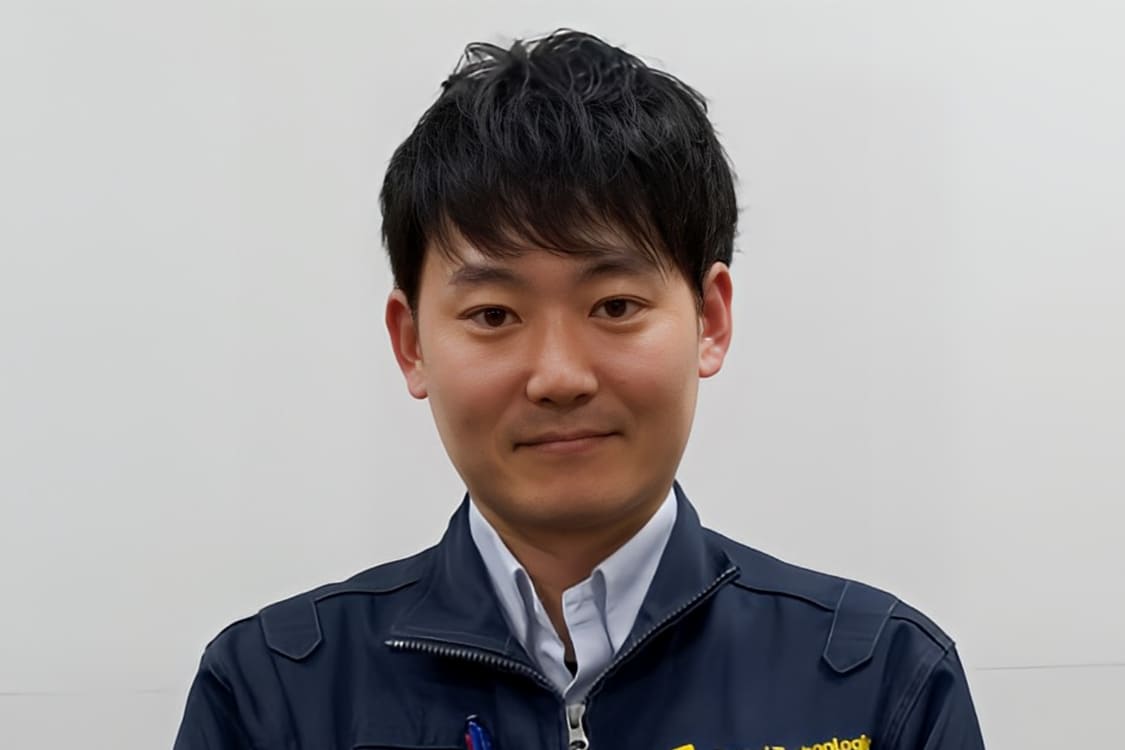
Mechanical Engineer.
Performed strength calculation and drawing preparation for the tower structure and mechanism, facilitated design verification in factory manufacturing processes, and served as supervisor for on-site installation.

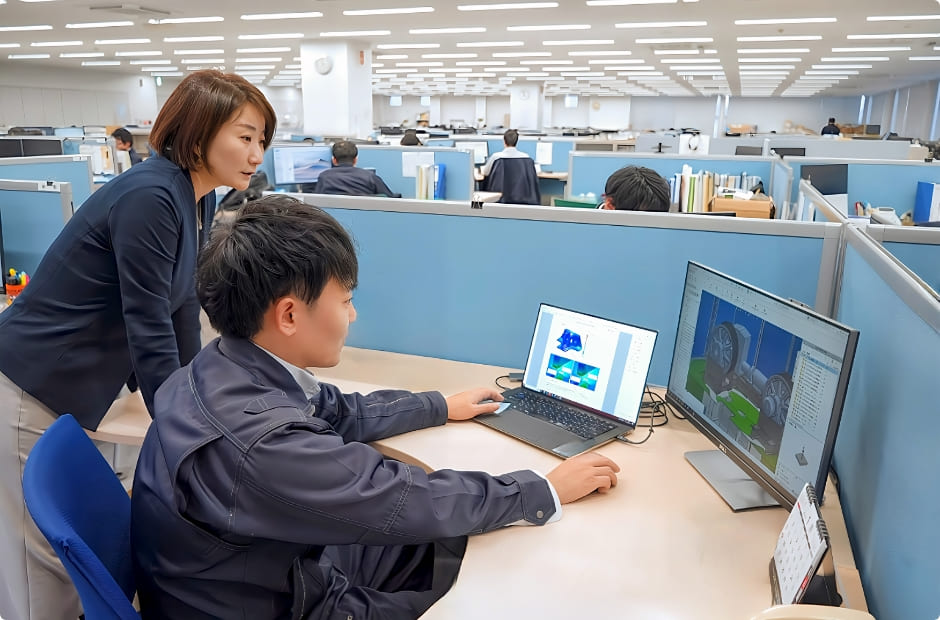
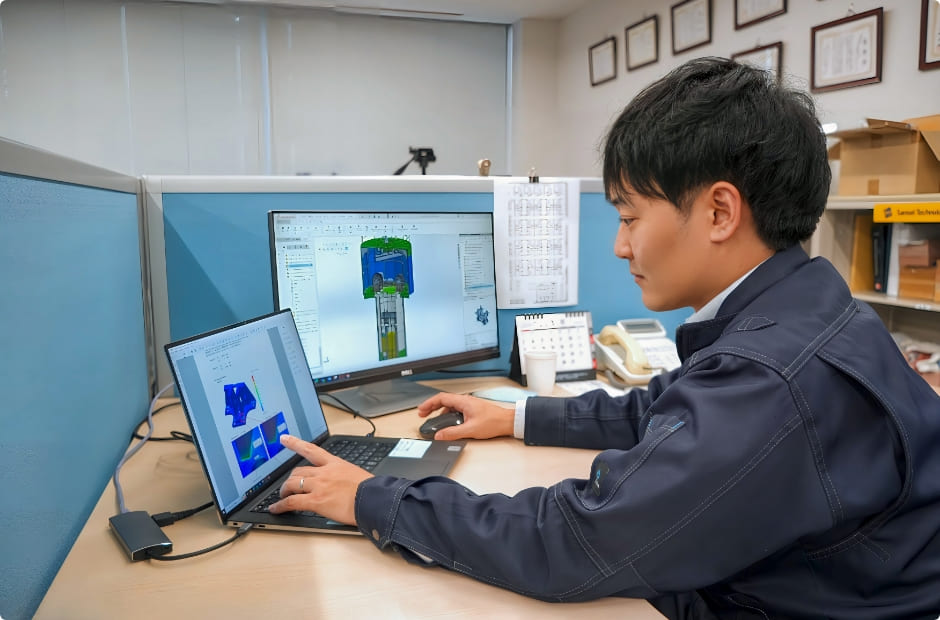
Creating Shapes Out Of Client’s Voices &Reliable Engineering To Go Beyond
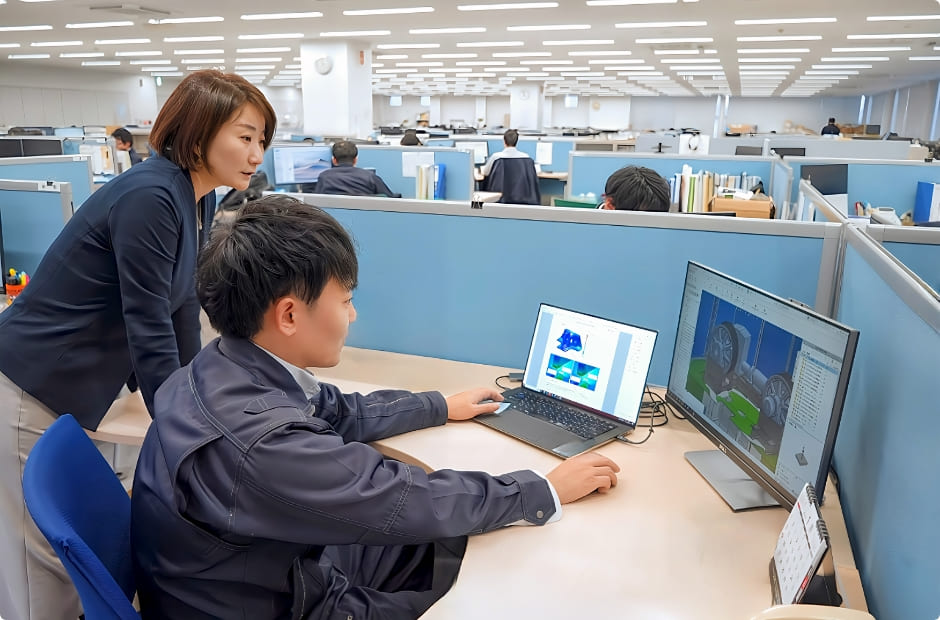
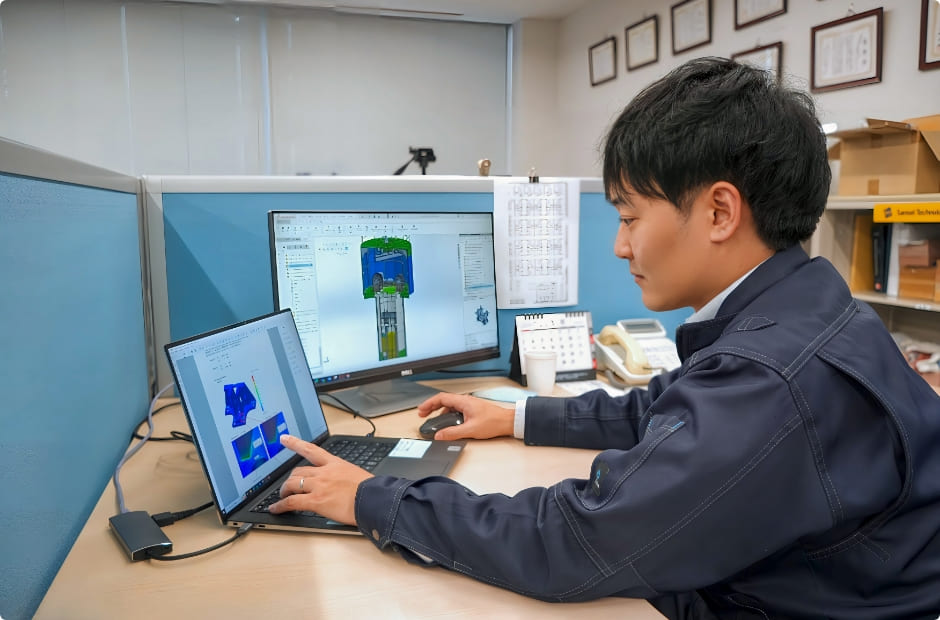
M.T
Difficult part was hearing from the client to understand what it was that they wanted in terms of technical specification, and researching information such as local requirement of South Korea to deliver Sansei’s ride system from Japan.
My role was to represent both side; speak for the client to Sansei departments or vice versa. It is always difficult to coordinate the client’s needs and technical limitations of Sansei departments for engineering and production.
So, I was constantly consulting Y.T. and we worked in collaboration to proceed with the project.
Y.T
South Korea has their own building codes and load calculation methods that are different from those of Japan. Therefore, the client provided us specifications that said “Korean Building Code” beforehand. It was all written in Korean and English, so I had to translate section by section to read. If I found any difference from Japanese code, I had to review the design of the structure to comply with the building code of South Korea.
After some experience, I really feel that learning never ends in this job. By the way, I took this opportunity to modify the tower design to conform to EU norms as well.
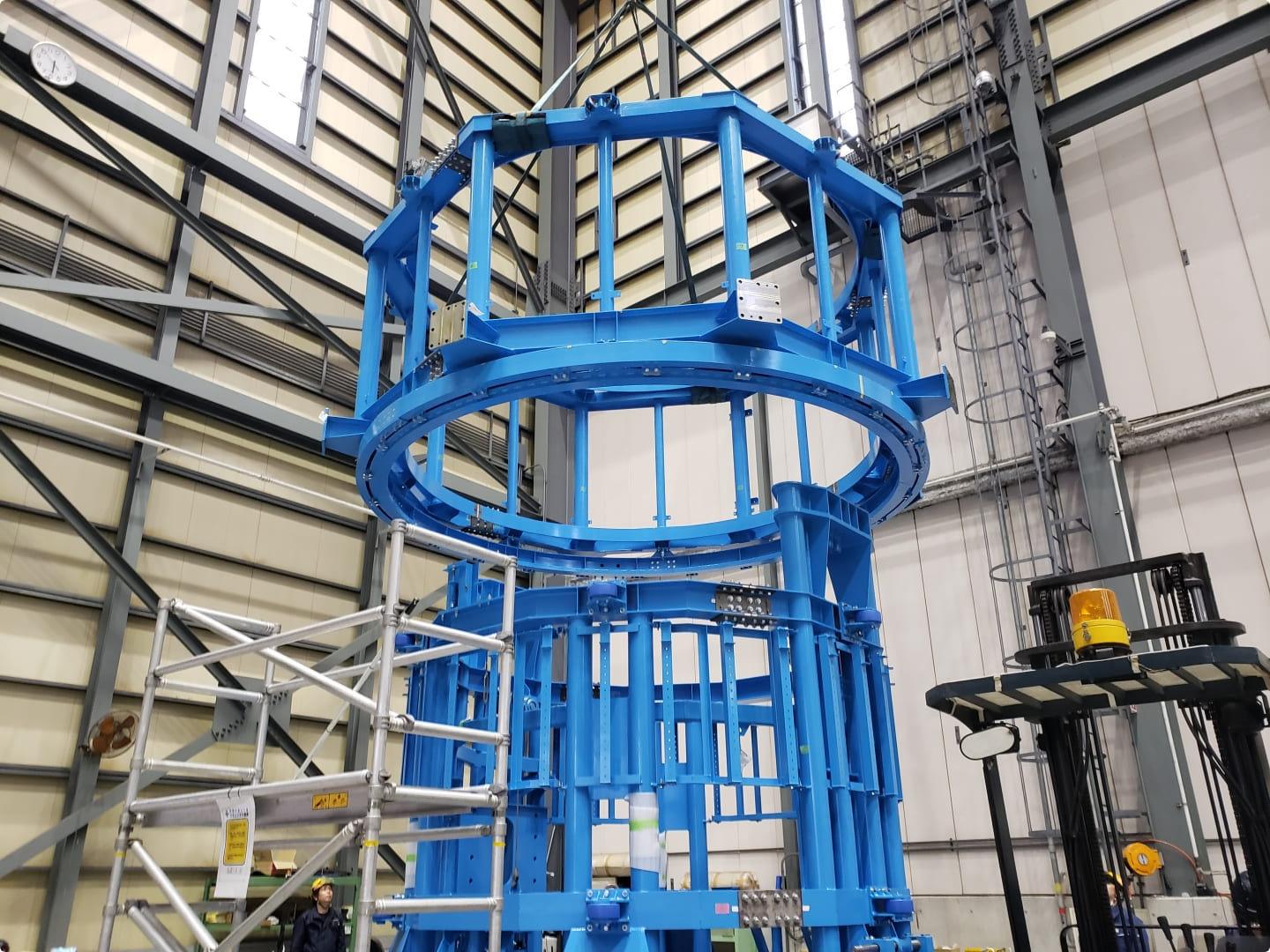
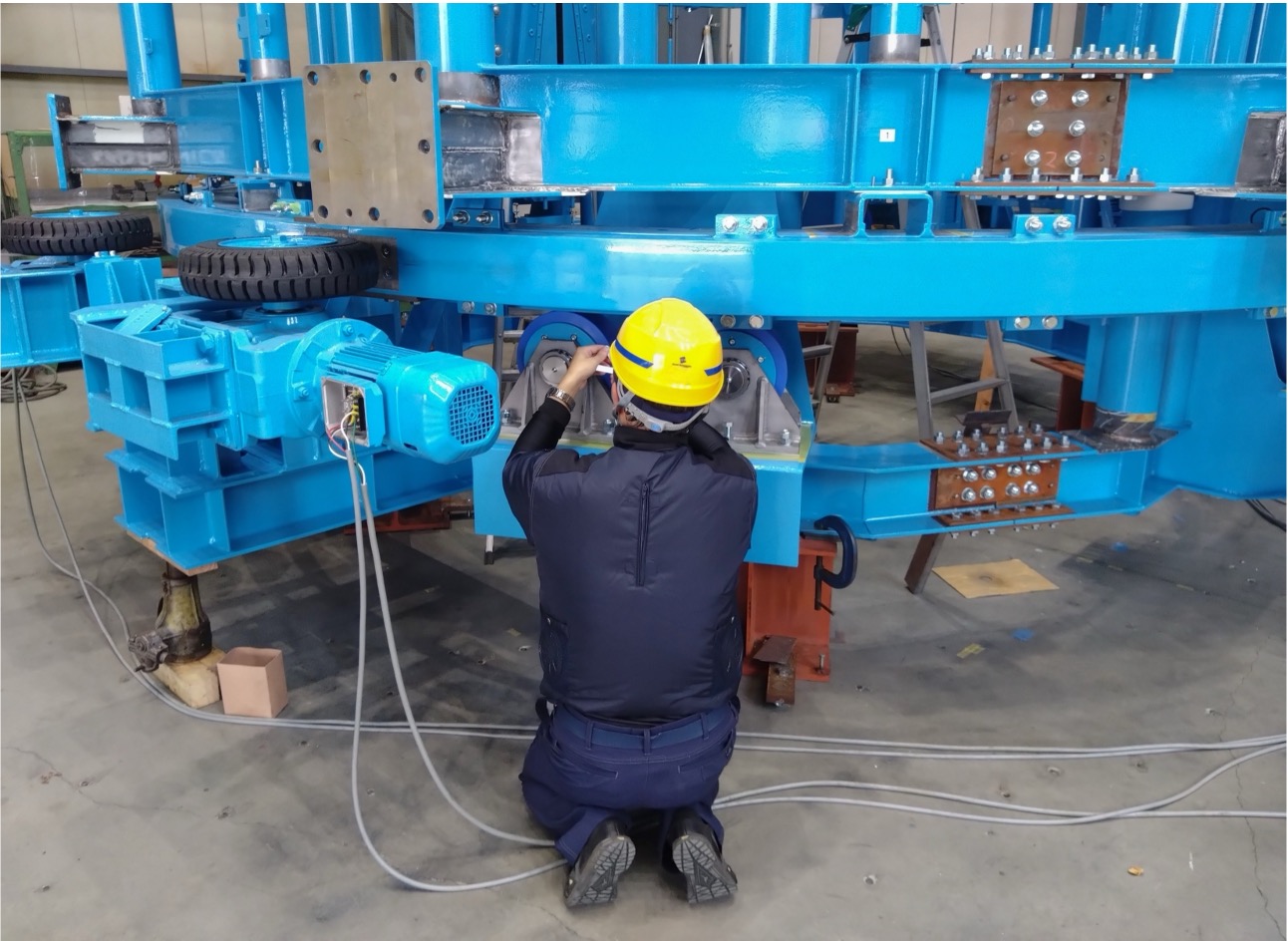
Quality Ensured Through Every ProcessAttention To Details For SafetyCovid-19 Challenges
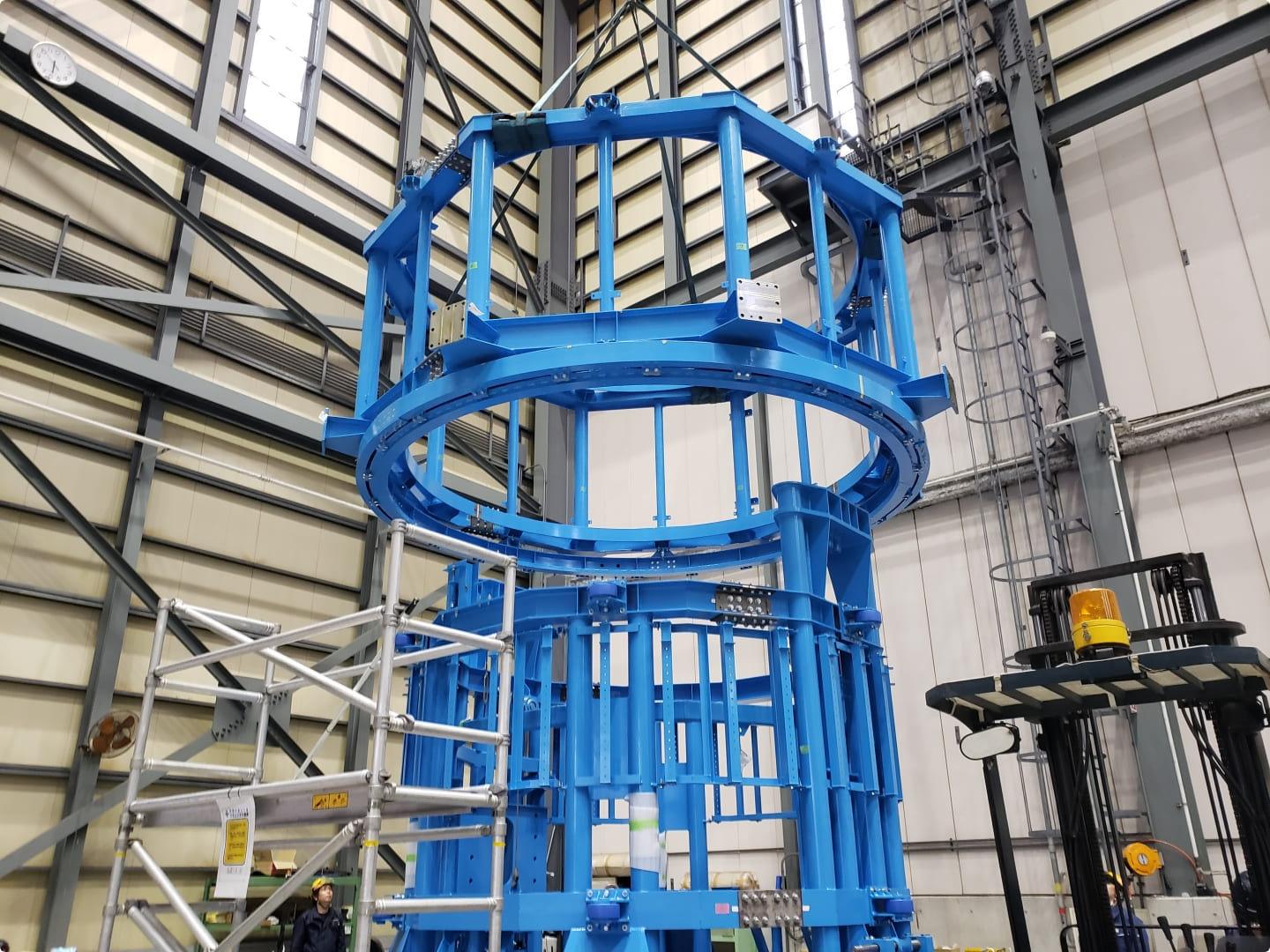
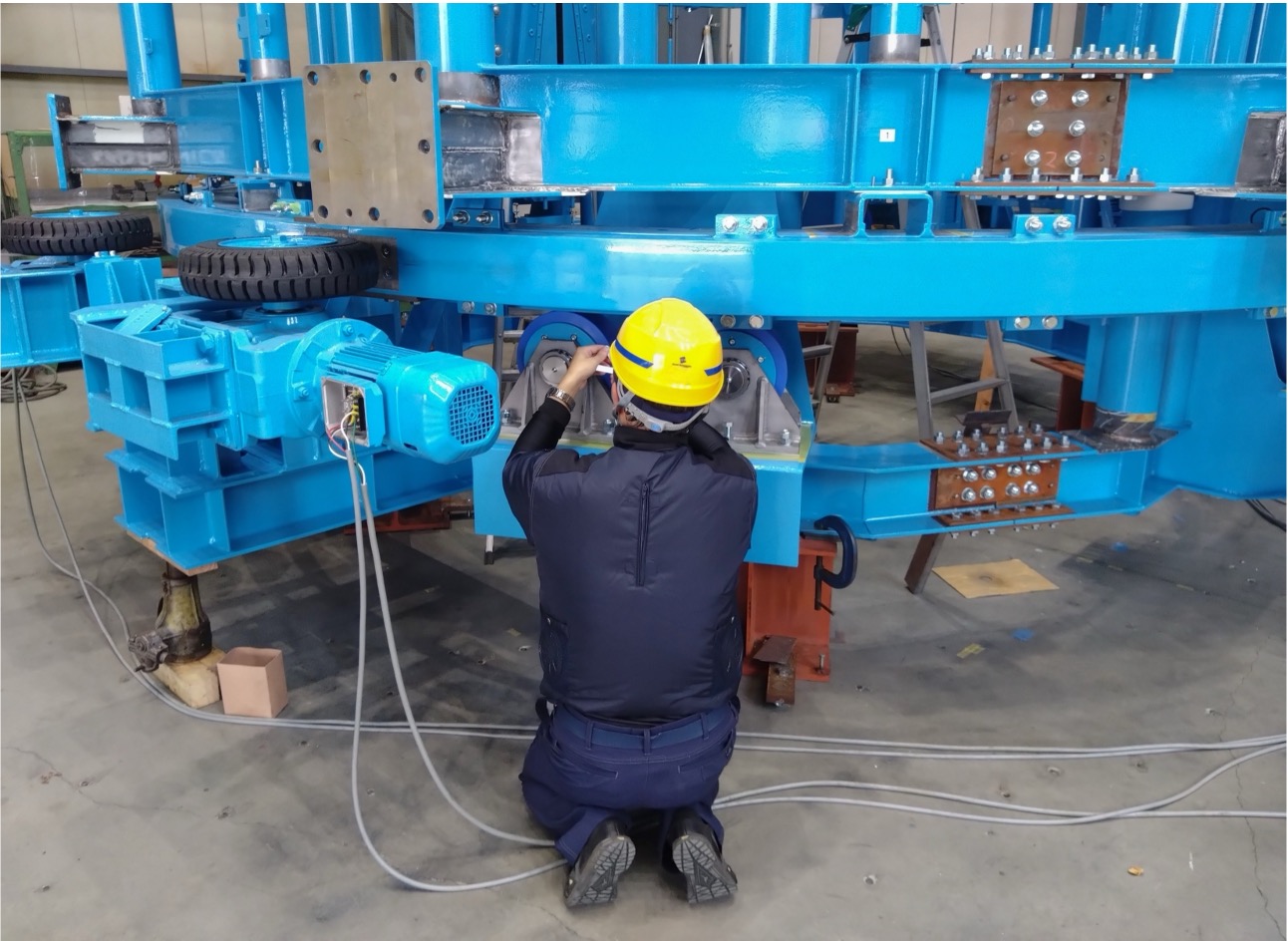
Y.T
Soon after the fabrication started, the pandemic of Covid-19 began. Some parts were being manufactured at associated shops, but because traveling was restricted, we could not perform production control and inspection of completed products as planned. We also had some parts fabricated in China.
Usually, we would travel to the factory for testing and inspection, but we had to do it online. Today, online checking has become more common, but in those days, product verification was mainly performed first hand and in person. So, at first, I was very skeptical, wondering “Is this really going to work?”
M.T
Due to the pandemic, we had to change many processes. This impacted original project schedule so much.
Especially noteworthy was the difficulty we faced with overseas travel restriction for engineers. It took time and effort to coordinate all required documentation and procedures appropriately. And, it was extremely tough to negotiate client on cost management.
For temporally assembly of this kind, most client would come to Japan to witness the testing at Sansei’s factory. But for this project, it was not possible for them to travel, so we had to carry out the factory testing without witness of the client.
Y.T
That’s right. Cabin rotation was tested at Sansei’s factory. Under the special circumstances, the client could not check the product themselves before shipping. So, we carried out the factory testing with the utmost care for client to feel assured.
It was an assembly test without cabin. All the necessary frames and mechanisms required for rotation were assembled and functions were tested. We thoroughly checked every detail, including proper movement of rotation rollers and made sure there was no abnormal noise from the drive mechanism.
I confirmed with my own eyes that each component was manufactured per design specifications, one by one. So, I was with confidence when I gave approval for shipping the products to the site.
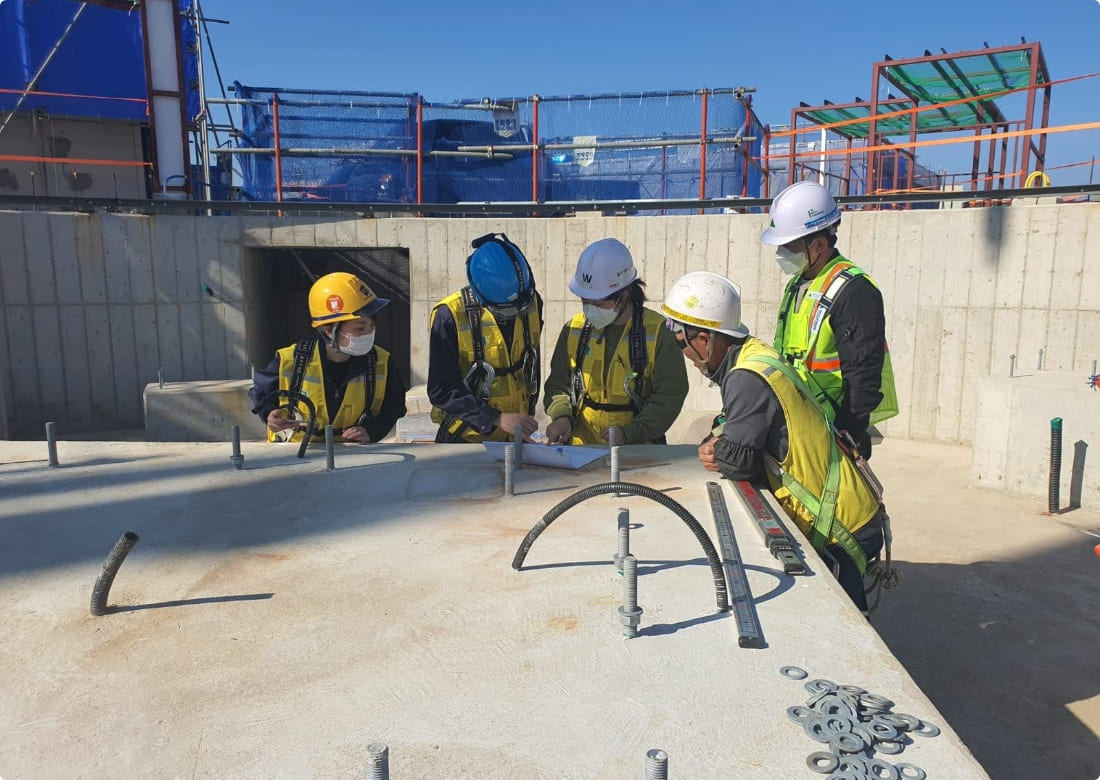
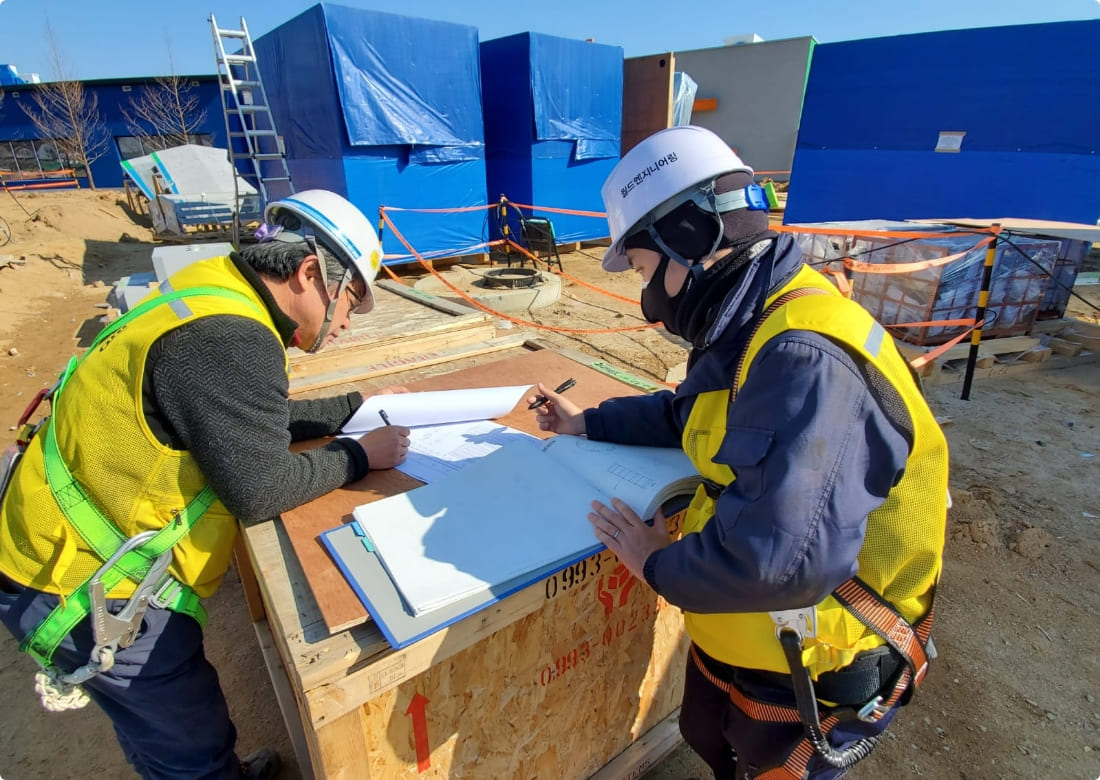
Outcome Accomplished By Team EffortOvercoming Language Barrier &Building Trust with Local Site Staff
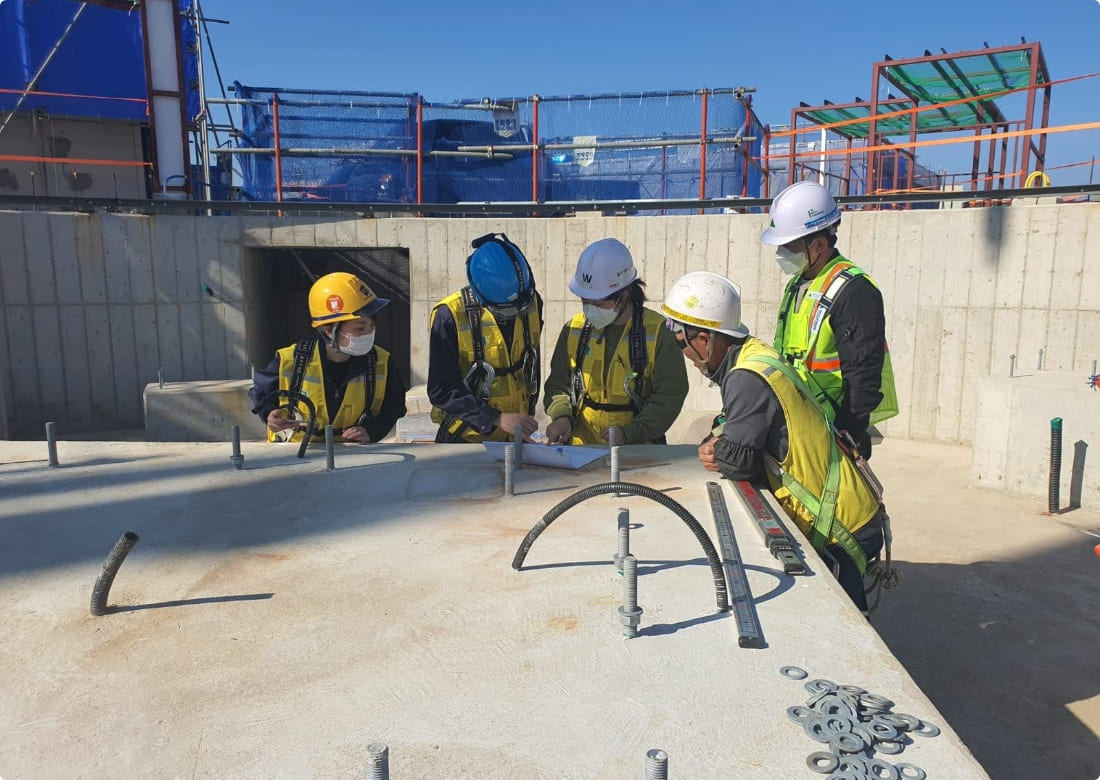
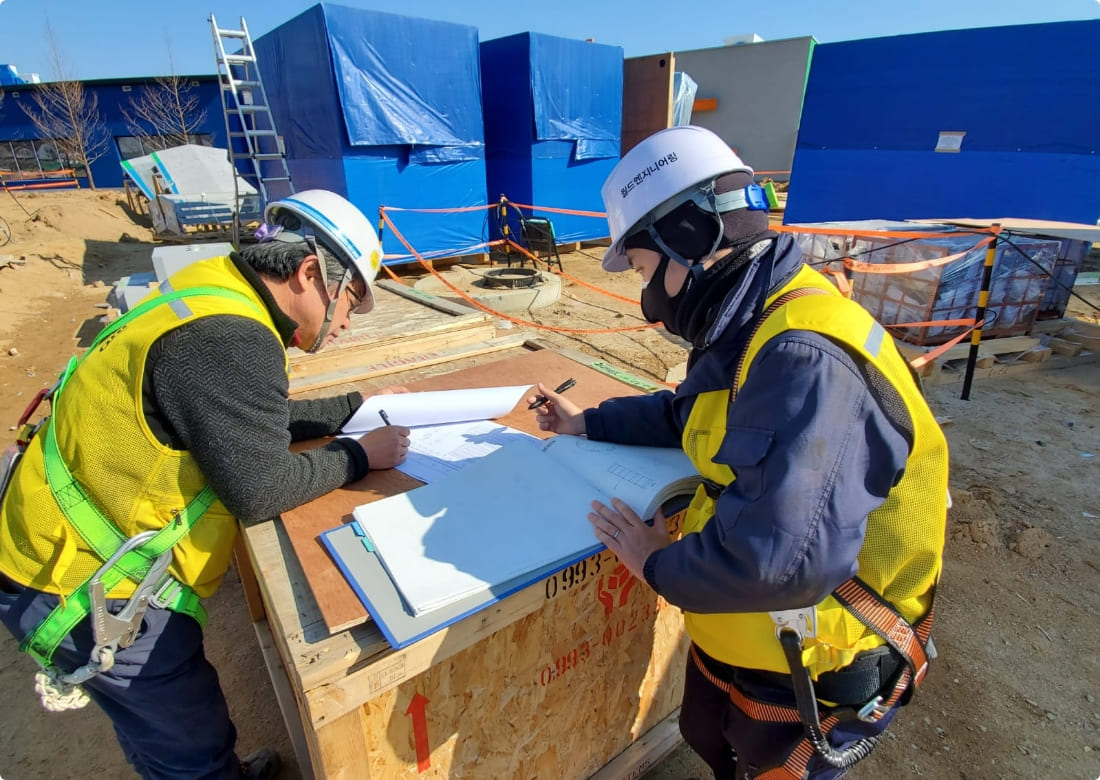
Y.T
In overseas installation projects, the actual work is carried out by local contractors, while I act as a supervisor to ensure that the installation is done per design specifications and provide guidance as needed. However, when I wanted to explain the design requirements to on-site workers, language barriers could sometimes lead to misunderstandings. This project was not any exception, and there were instances where the president of the contractor company and I had different opinions, leading to conflicts.
Still, after the day’s work, we would have dinner together and enjoy relaxing moments. Through such experiences, I strongly felt they were colleagues who supported me on-site, working together to bring about a successful outcome.
M.T
At the site, other manufacturers equipment was also under installation. So, sometimes, Sansei tower team didn’t have enough personnel needed for our tower installation, and work schedule was delayed. In such cases, I had to make careful adjustments with the client and the installation contractor. Looking back now, those were very tough days. However, Y.T. and other team members sent me daily reports on the status of site work, and it was a great help in negotiations and adjustments.
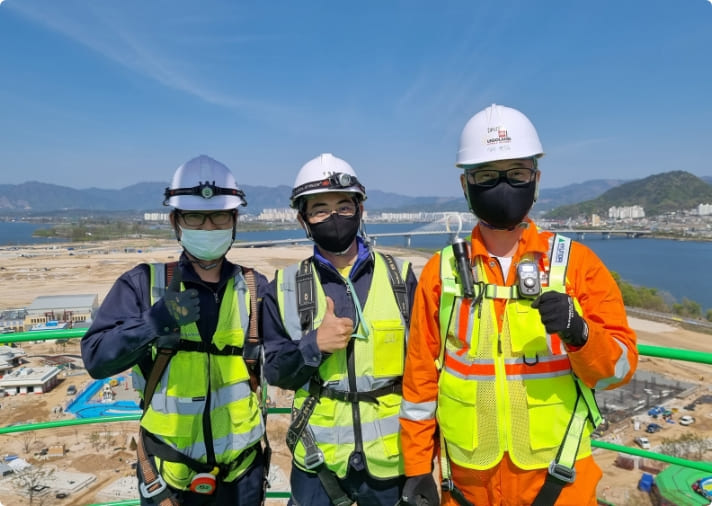
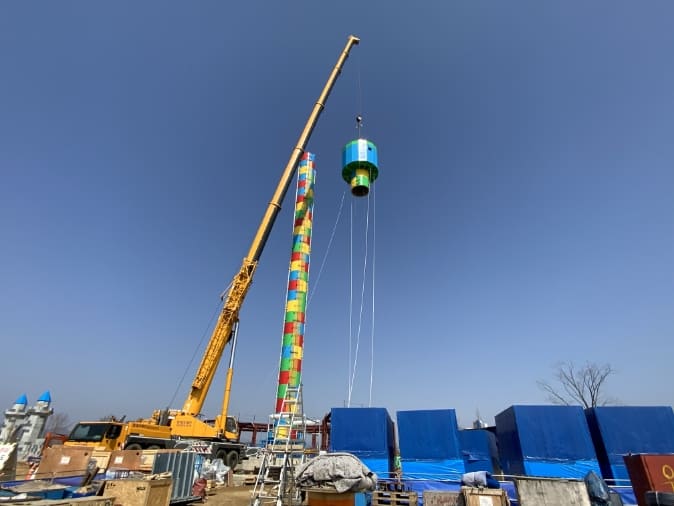
Clearing Nervous Moments Altogether &Quality Assured By Precise Assembly
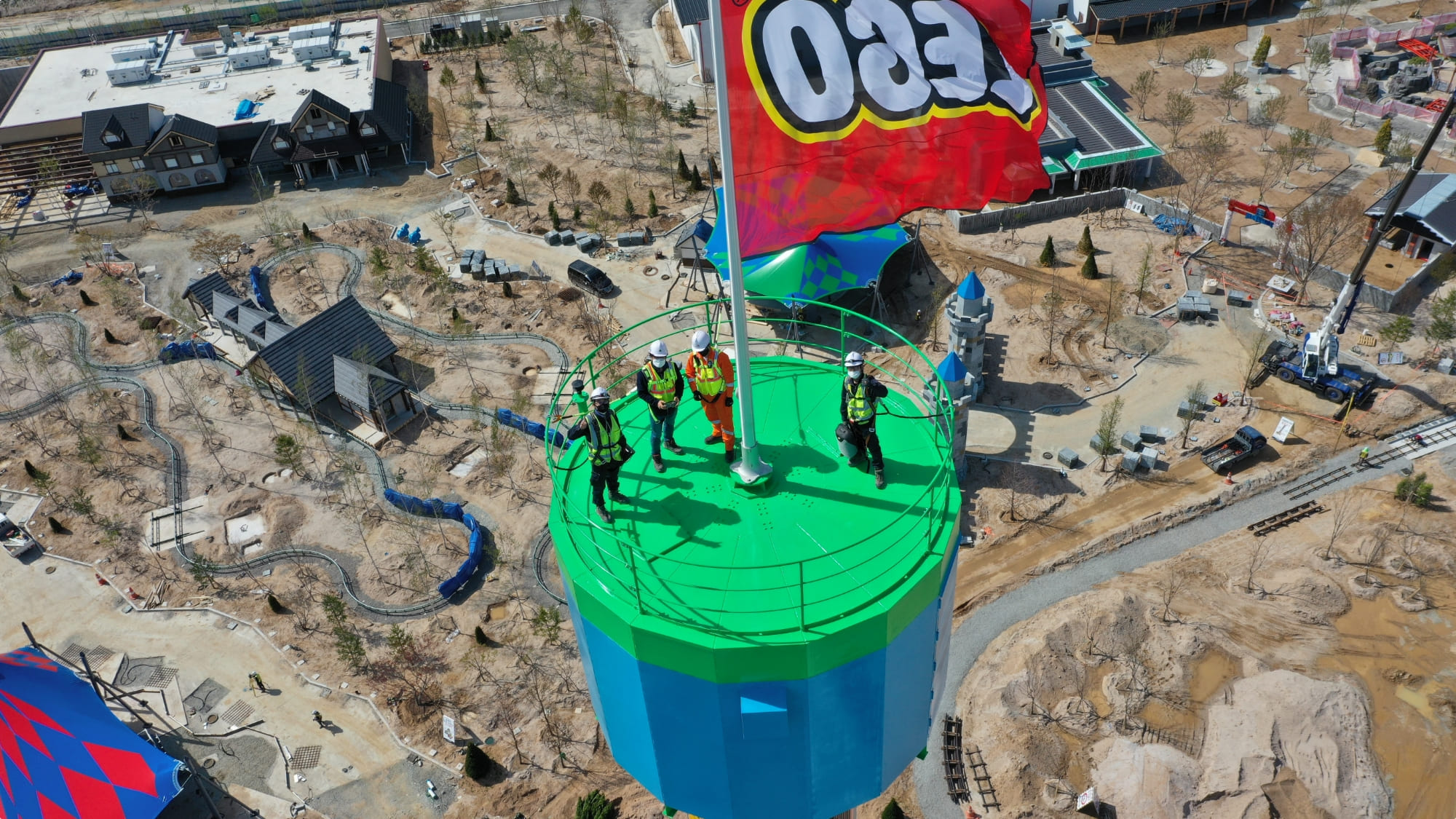
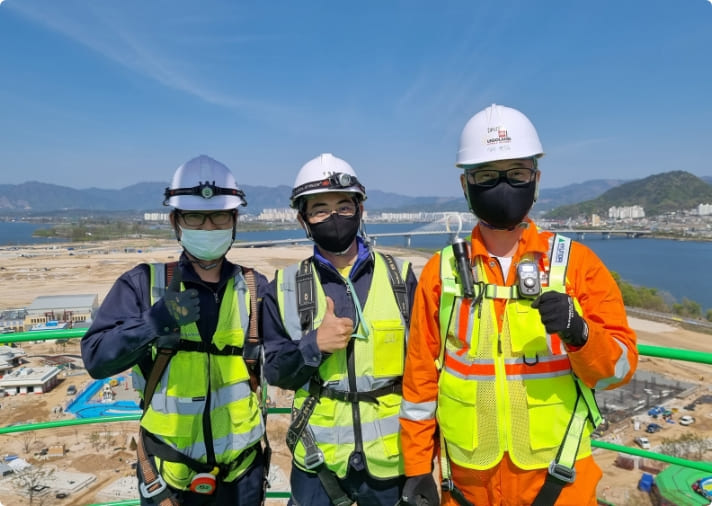
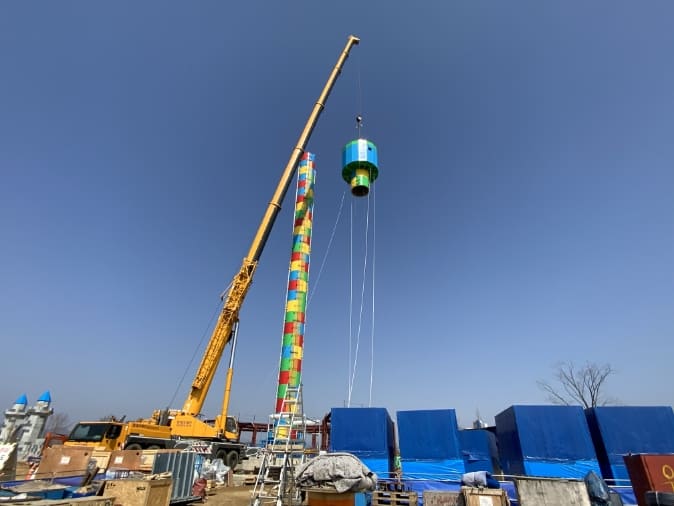
Y.T
The most nerve-wracking part of the on-site work was the installation of the machine room. This unit requires some field welding of components before installation. After assembly on the ground level, the whole unit is hoisted up by a crane to a height of approximately 50 meters above ground, then, precisely placed on top of the tower structure.
As it is an extremely heavy structure, the whole site was very nervous while the lifting operation took place, creating a tense atmosphere throughout the work site. Everyone was holding their breath. We all watched intently from the ground, unable to take our eyes off the operation for even a moment.
Finally, when the LEGO symbol flag was raised at the top of the tower, cheers naturally erupted, and we all shared a sense of relief and accomplishment.
Y.T
The cabin was manufactured in eight sections, but eventually they would be put together on site to form a doughnut shape. Therefore, if the mating surfaces were out of alignment even by a few millimeters when assembling each section, the final piece would not fit properly. Moreover, this is a part that guests can see, so I remember how everyone took great care as we worked on details.